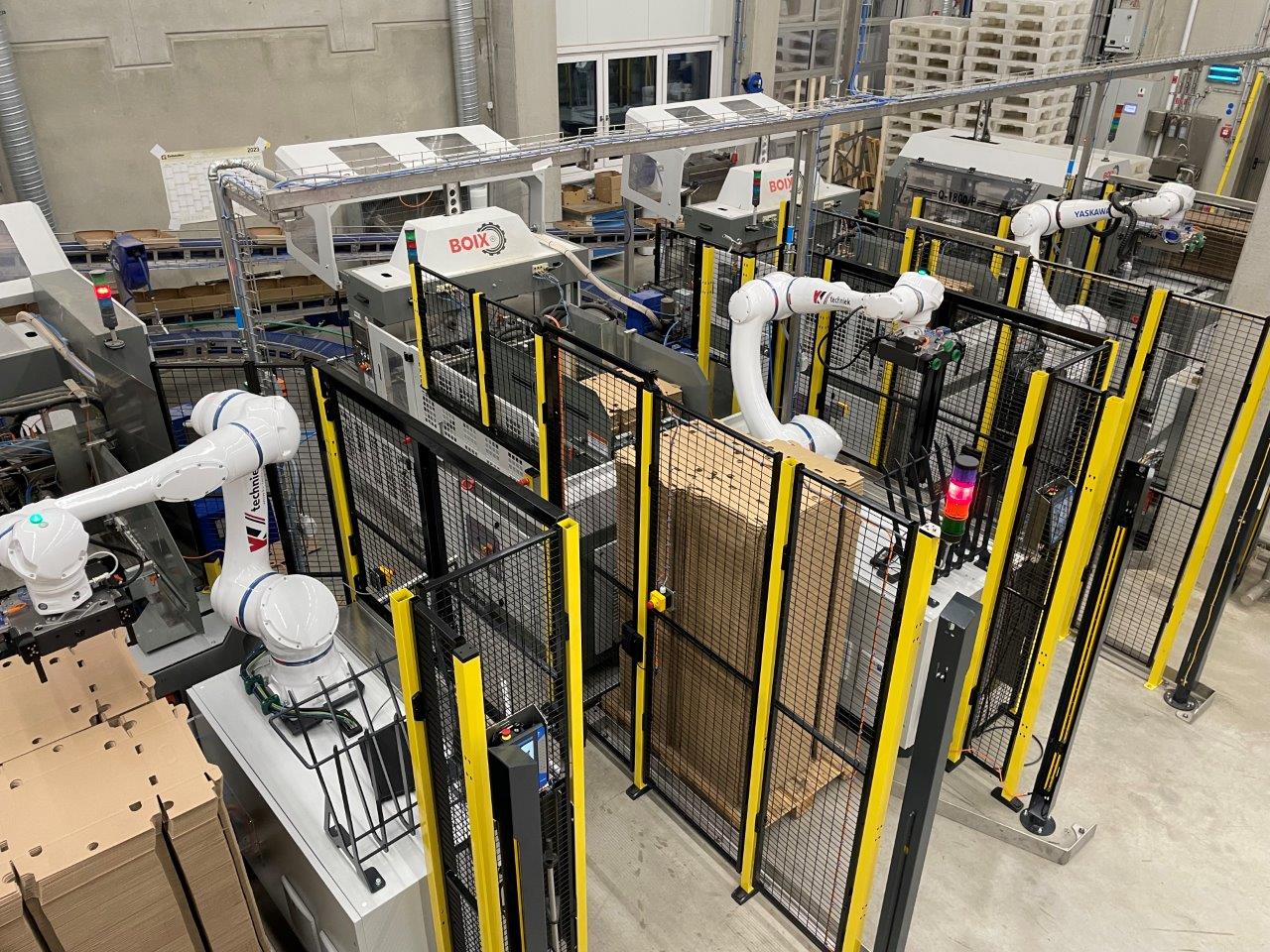
‘Cobots in de verpakkingslijn worden steeds breder toepasbaar’
Door kwalificaties als ‘eenvoudig programmeerbaar’ en ‘veilig zonder hekwerk’ ziet menig eindgebruiker cobots als alternatief voor robots om een verpakkingslijn te automatiseren. In de praktijk gaat die vlieger meestal niet op, leert een rondje langs robot- en cobotfabrikanten Fanuc en Yaskawa, en systemintegrators KV Techniek en Robertpack. Cobots zijn in de verpakkingswereld vooral een aanvulling op robots; ze gaan ze niet vervangen.
Picking, packing, palletizing. Dat zijn de drie domeinen waar je als automatiseerder van een verpakkingslijn met een robot of cobot een flinke slag kunt maken. ‘Bij picking is vaak sprake van hoge snelheden, vooral in de food-lijnen waar tot wel 400 producten per minuut worden verwerkt. Om dat te behappen zijn meerdere robots nodig, die in het beste geval 100 slagen per minuut kunnen maken. Bij packing zou je ook cobots kunnen inzetten, mits dat verpakken niet te snel gebeurt, maximaal zo’n zes tot acht manipulaties per minuut. Diezelfde ordegrootte geldt voor cobots aan het einde van de verpakkingslijn, bij het palletiseren’, schetst Filip Tuypens, office manager van Fanuc Benelux, het speelveld voor robots en cobots in verpakkingstoepassingen.
Cobots zijn veilig
Cobots onderscheiden zich qua veiligheid van robots doordat ze zijn uitgerust met gevoelige krachtsensoren, waardoor de cobot na een collisie razendsnel wordt stilgezet. Dat maakt hem geschikt om zonder hekwerk samen te kunnen werken met mensen, al gelden daar naar zeggen van Job ten Berge, salesmanager bij systemintegrator Robertpack, wel beperkingen voor. ‘Dat een cobot stopt bij een collisie wil niet zeggen dat het direct veilig is. Iedereen moet voldoen aan de CE-norm waar onder andere de veiligheidsnorm in beschreven staat. Bij cobots zonder hekwerk is het opmaken van een gedegen risico-analyse ingewikkelder dan bij robots omdat tijdens productie een persoon in aanraking kan komen met de cobot. Je moet onder andere rekening houden met klemgevaar, hoe je het product oppakt en de maximale impact die het product mag uitoefenen op een persoon. Dat laatste aspect is variabel. Zo mag de impact op benen hoger zijn dan op het hoofd en moet je er ook nog rekening mee houden dat niet iedereen dezelfde lichaamslengte heeft. De snelheid van de cobot, de grijperuitvoering, het product dat de cobot moet verwerken en de omgeving waarin de oplossing staat, spelen daarom een grote rol bij het bepalen of de cobot veilig zonder hekwerk mag werken. Cobots zien wij als een goede aanvulling op robots voor met name eenvoudige toepassingen met een wat lagere capaciteit. Denk aan palletiseren van dozen waar wij een standaardoplossing voor hebben ontwikkeld met een payload tot 30 kg.’
Flexibel inzetbaar
Als kan worden voldaan aan de voorwaarden voor veilige toepassing kan de cobot flexibel worden ingezet. Dat is ideaal voor verplaatsbaar werk, bijvoorbeeld de ene keer op lijn 1 en de andere keer op lijn 2. ‘Een cobot leent zich ook goed om in bestaande lijnen te worden geïmplementeerd omdat er geen afscherming naast of overheen hoeft te worden geplaatst. De configuratie met een cobot maakt de lijn minder gevoelig voor verstoringen door de operator, wat voor een betere toegankelijkheid zorgt. Ook kun je zo compacter bouwen’, licht Eddie Mennen, managing director van Yaskawa toe. ‘Samen met ontwikkelingen als foodgrade-uitvoeringen en speciale cobots voor ruwe omgevingen, worden de cobots steeds breder toepasbaar.’
‘Cobots zien wij als goede aanvulling op robots’
Snel en veilig
Weinig ruimte en te snel voor een veilige cobot-modus. Daar lag de uitdaging voor systemintegrator KV Techniek om voor een klant in Duitsland bij vijf lijnen tot een cobot-oplossing te komen voor het geautomatiseerd beladen met plano’s van een tray-vouwmachine. ‘De HC20-cobots van Yaskawa hebben we afgeschermd met een hekwerk. We kunnen ze ook uitvoeren met safety scanners, als cobot zonder hekwerk. Maar de ruimte bij de klant was hiervoor niet geschikt, omdat er regelmatig mensen heel kort langs de machine lopen. Dat is dan niet handig, want door stilstand ga je capaciteit verliezen. Als binnenkort de productieruimte anders wordt ingedeeld, kun je wel veiligheidsscanners gebruiken. Met de cobots kun je dan flexibel de lijn aanpassen. Bovendien passen we de nauwkeurige krachtopnemers van de cobot toe om te detecteren of we met een plano te maken hebben of een tussenvel. De plano heeft vier gaten waar de vingers van de grijper in aangrijpen. Is er een tussenvel, dan resulteert dat in een hoger koppel, wat bij een bepaald maximum het teken is om een volgende stap in het cobotprogramma te starten’, legt KV Techniek-directeur Bastiaan Krijger uit.
Optimale oplossing
Voor KV Techniek is dit het eerste project met Yaskawa-cobots. ‘We doen vaker met Yaskawa projecten, maar voorheen was dat met robots. Ook werken we met Fanuc en ABB. Dit hangt vaak samen met wat de klant al gebruikt; daar hebben ze dan ervaring mee. Als een project op een vorig project lijkt dat we bijvoorbeeld met een Fanuc hebben uitgevoerd, dan opteren we uiteraard weer voor een Fanuc. Dan kun je makkelijk de software overschieten.’
Dezelfde insteek is er bij Robertpack. ‘We gaan altijd voor de optimale oplossing, of dat nu met robots of met cobots is. We zijn overigens relatief laat met cobots gaan werken, omdat er naar ons idee nog geen cobots waren die in een industriële omgeving 15-20 jaar meegaan. Met de CRX-cobots van Fanuc (die 8 jaar onderhoudsvrij zijn, red.) en de HC-lijn van Yaskawa hebben we dat vertrouwen wel. We passen de HC20/30PL toe in onze kant-en-klare palletizer, die je zo kunt inklikken aan een rollerbaan. Binnenkort is de palletizer ook beschikbaar met de CRX’, aldus Ten Berge.
Zelf programmeren
De cobotfabrikanten steken veel energie om de technologie voor eindklanten toegankelijk te maken. Dat komt naar voren in gebruikersvriendelijke ‘drag and drop’-bedienings- en programmeertools. Een voorbeeld is de Palletbuilder-software van Yaskawa, die draait op de Smart Pendant, een intuïtieve robotcontroller op een 10 inch-touchscreen.
‘Een plus van cobots ten opzichte van robots is dat je het bewegingsprogramma met de hand kunt voordoen, waarop het bewegingspatroon automatisch wordt geprogrammeerd. Hiermee kun je ook gemakkelijk aanpassingen maken’, vertelt Tuypens van Fanuc. ‘Overigens ben je er dan nog niet, want voor integratie in de lijn heb je al snel te maken met een complexiteit die vergelijkbaar is met die van standaard robotcellen. Er is interfacing nodig voor de overdracht van signalen, vaak moet vision worden geïntegreerd, moeten er passende grijpers bij, enzovoorts. Hulp van een systemintegrator is dan geen overbodige luxe.’
Bastiaan Krijger beaamt dit: ‘Klanten zien wat er mogelijk is en denken dat ze het gemakkelijk zelf kunnen. Ga je dieper op de toepassing in, dan blijkt dat er nog heel wat rekenwerk achter zit dat door ons moet worden geprogrammeerd. Ook is het voor eindgebruikers lastig om bij te blijven met hun kennis. Aanpassingen of updates worden dus vaak bij ons uitbesteed.’
Dat ziet Job ten Berge ook. ‘We leveren software bij onze palletizer om zelf stapelpatronen te maken of het doosformaat aan te passen. In de praktijk hebben bedrijven daar niet de tijd en/of kennis voor en schakelen ze ons in. Omdat wij dat dagelijks doen gaat dat niet alleen een stuk sneller, maar levert dat ook qua bewegingspatroon het optimale resultaat op, wat weer ten goede komt aan de levensduur van de cobot. Door onze klanten in het programmeren te ontzorgen komen ze ook niet voor verrassingen te staan wat betreft veiligheid.’
Meer artikelen
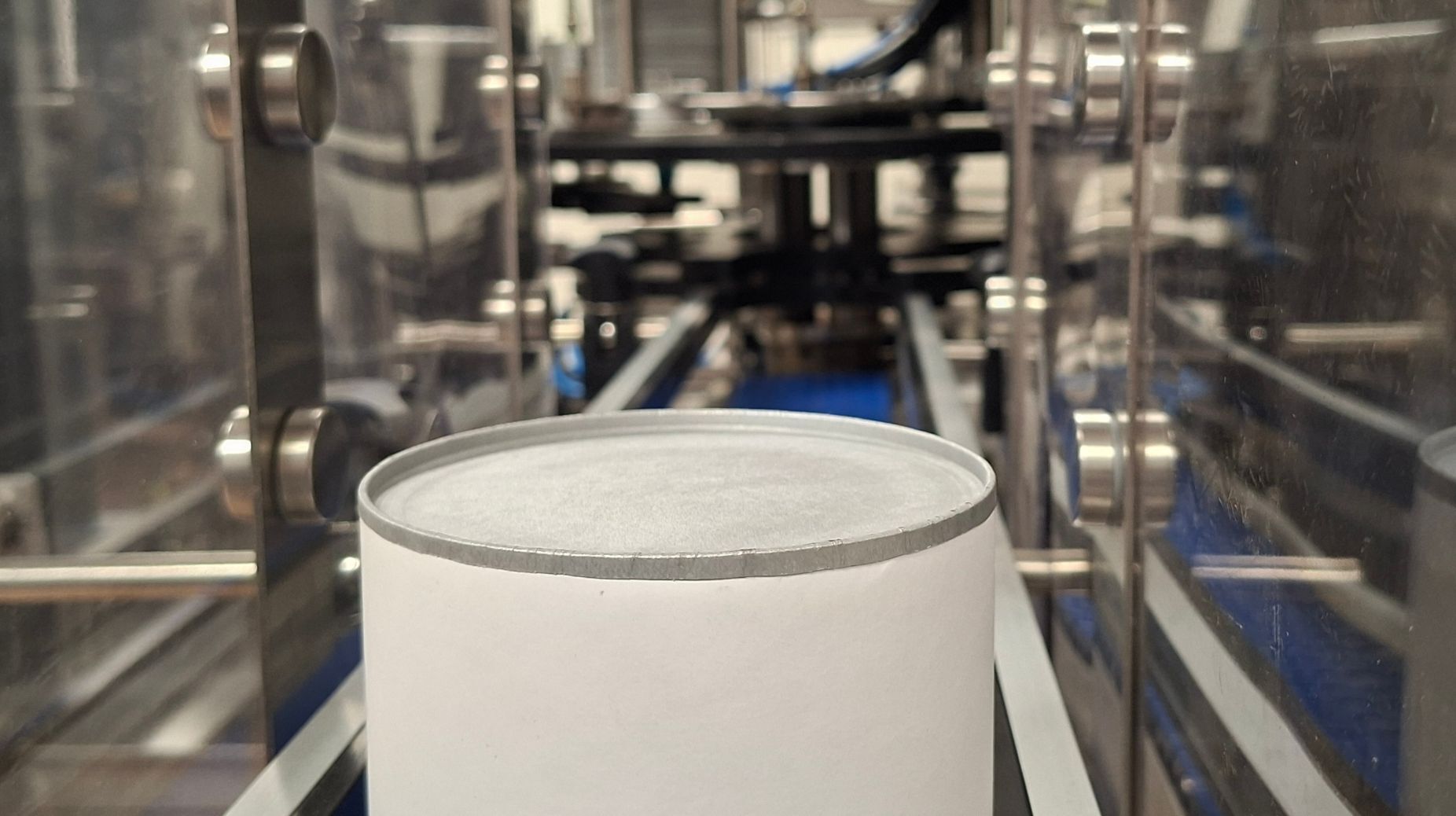
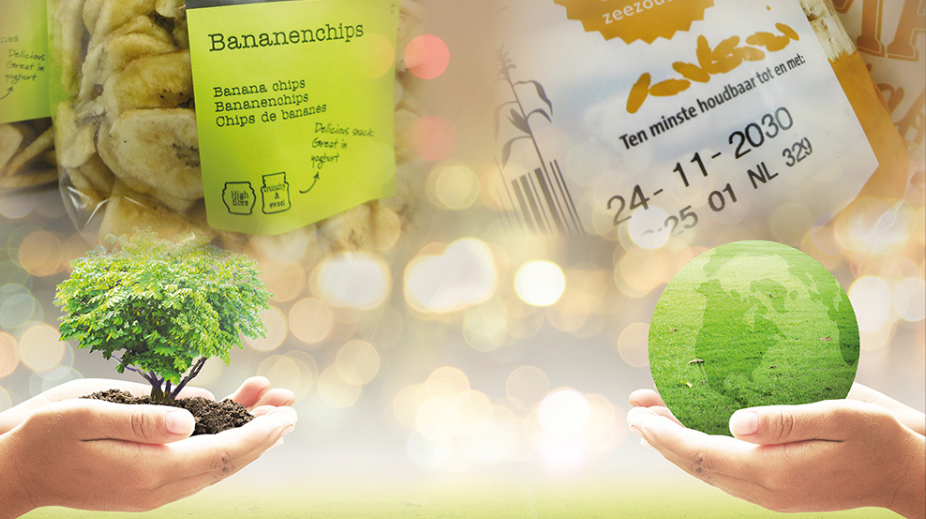
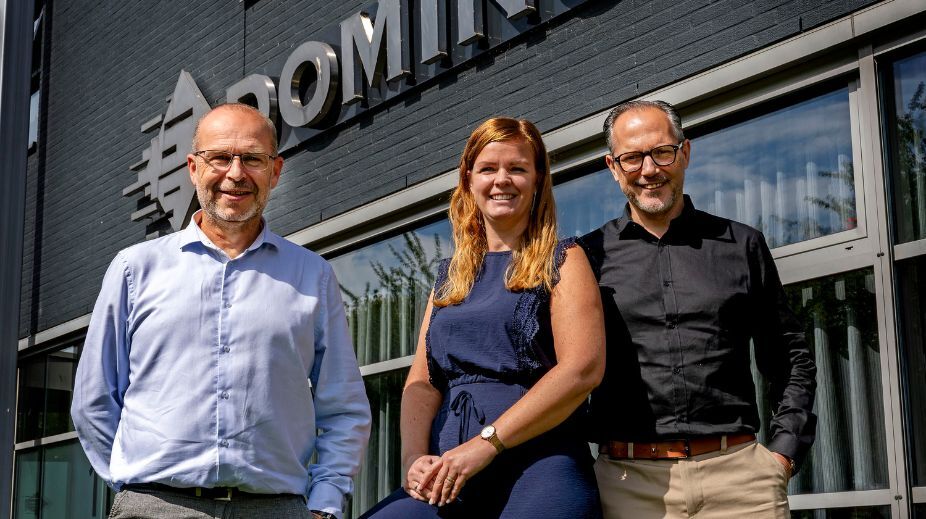
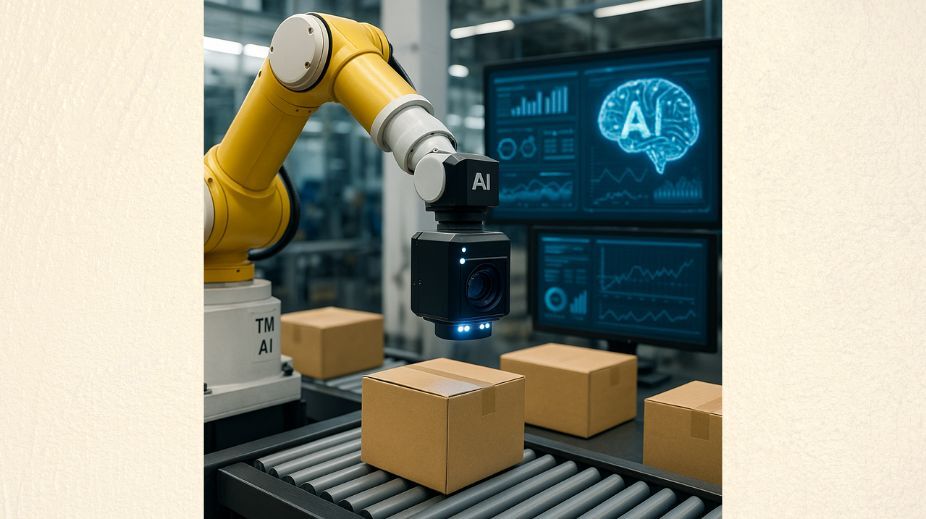
Gerelateerde artikelen
Papieren bodems voor kartonnen kokers bij Dutchpacks op FachPack
Het in Roosendaal gevestigde Dutchpacks ontwikkelt machines voor de verpakkingsindustrie en...
De Koningh ziet etikettering als strategische schakel
De tijd dat etikettering slechts een operationele stap aan het einde van het verpakkingsproces was,...
QR Code powered by GS1 heeft grote impact
De QR Code powered by GS1 moet vanaf 2027 wereldwijd inzetbaar zijn aan de kassa. Dit heeft grote...
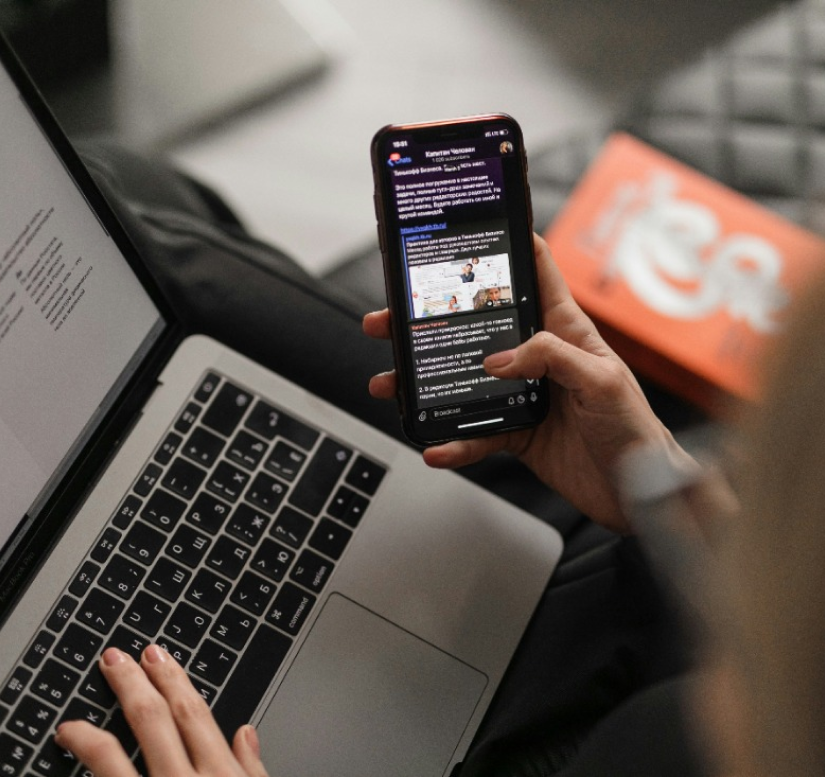
VM nieuwsbrief
- Blijf op de hoogte met het laatste nieuws uit de verpakkingsindustrie
- Techniek, duurzaamheid, design en meer
- Gratis in jouw inbox