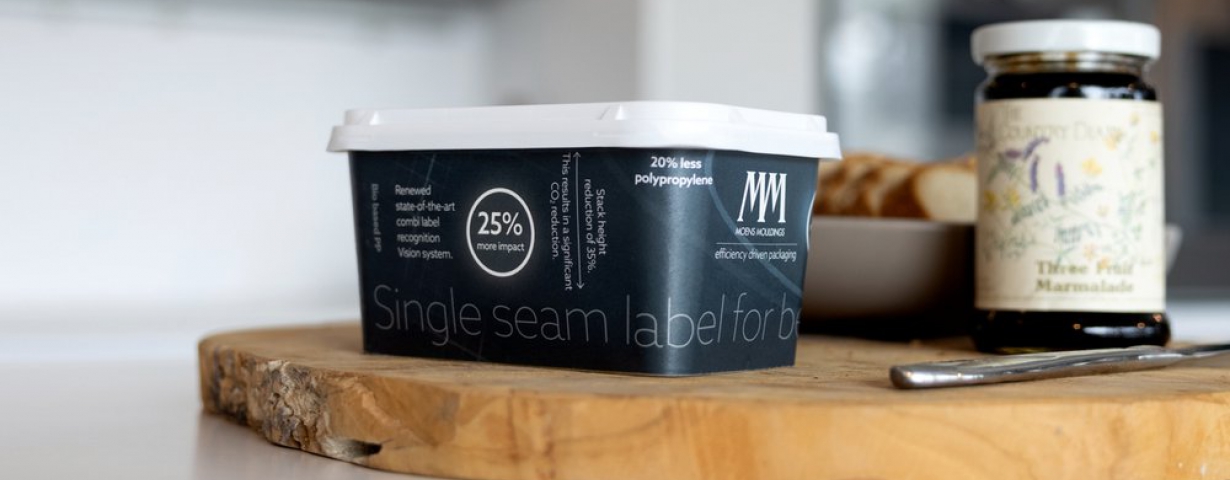
Margarinekuip sterk afgeslankt
Moens Mouldings uit Beverwijk heeft een spuitgiettechniek en bijbehorende -robot ontwikkeld om sneller en lichtere in mould labeling (IML) verpakkingen te produceren. Na diverse lightweighting projecten is alle kennis gebundeld in een geoptimaliseerde 500 grams margarinekuip die minder plastic gebruikt en de productiekosten verlaagt.
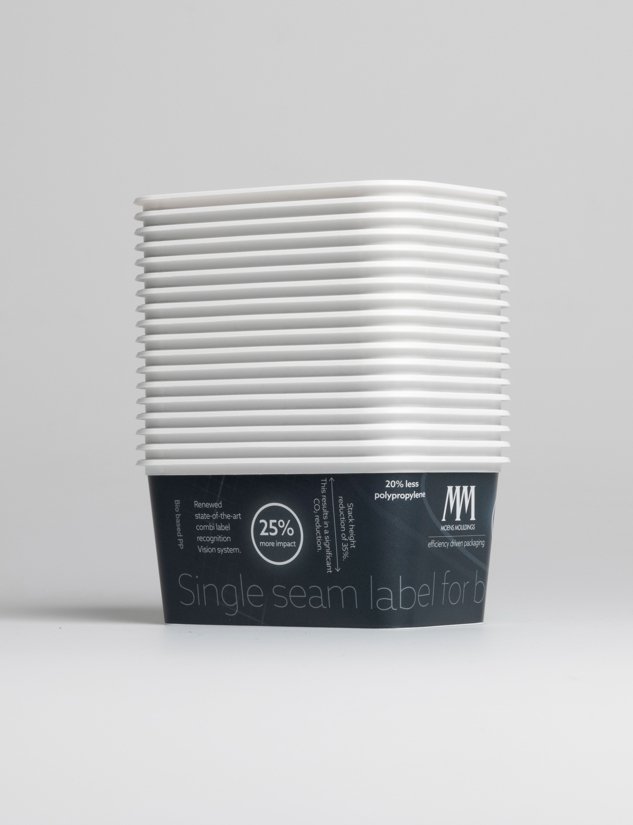
Met enige trots zet algemeen directeur Wim Moens de nieuwe 500 grams margarinekuip op tafel. Het nieuwe model lijkt in eerste instantie op de vele margarinekuipjes die je ziet in het winkelschap en op de eettafel. De bijna onzichtbare verschillen zijn echter enorm. Slimme constructies, een nieuwe productietechniek en een uitgekiende materiaaldosering zorgen ervoor dat de nieuwe Moens-kuip fors minder weegt dan de bestaande kuip. Het gaat hier om hightech engineering voor massaproductie waarbij het ontwerpteam zo’n 20% polypropyleen heeft bespaard en enkele functionele verbeteringen heeft doorgevoerd waardoor de kuip meer gewicht kan dragen en leeg gestapeld minder ruimte inneemt.
Wanddikte margarinekuip reduceren
Wim Moens gaat in op de techniek: ‘Je kan niet zomaar de wanddikte van een IML-bakje reduceren, want dan raak je de functionaliteit kwijt. De stapelsterkte verandert, de wand kan bol gaan staan, et cetera. Er is veel ontwerpervaring nodig en je hebt goede simulatieprogramma’s nodig om tot de juiste resultaten te komen. Wij hebben de afgelopen jaren flink geïnvesteerd in softwareprogramma’s die steeds beter de werkelijkheid reproduceren.’
‘Aan de hand van de vereiste specificaties van het kuipje maken we de wanddikte functioneel. Bij de randen en hoeken dikker dan bij de wanden, bijvoorbeeld. Daarnaast zijn er constructieve verstevigingen nodig, zoals een rechte wand op de bodemhoeken die zorgt dat de kuip nog sterker wordt in plaats van de gebruikelijke ronde hoek. Een andere constructieve verbetering is de holle wand in de bovenrand, een soort honingraadconstructie. Die zorgt voor de nodige sterkte bovenin.’
Optimale kuip
Het is een optelsom van kleine verbeteringen en optimalisaties die zorgen voor een optimale kuip, vertelt Moens. ‘Uiteindelijk zijn we bij de 500 grams margarinekuip van 14,5 gram naar 11,88 gram gegaan, terwijl de topload zelfs verhoogd is van 25 kg naar 40 kg. Wanddikte is dus niet één op één in relatie met de kuipsterkte.’
Verder is de nestbaarheid van de nieuwe kuip fors verhoogd waardoor de stapelhoogte 35% lager is en er meer kuipjes op een pallet passen.
Een andere optimalisatie zit in het etiket dat van een kruisvorm, bestaande uit één bodemetiket met daaraan vast vier zijetiketten, is teruggebracht naar één bodemetiket en één los rondometiket. Dat oogt mooier, want aan de zijkanten is slechts één naad zichtbaar in plaatst van vier naden en het bespaart productieafval.
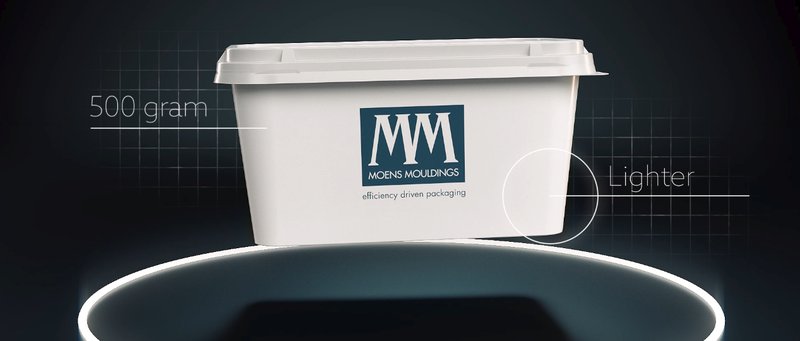
Dicht IML-etiket
Terug naar het begin. Met het simpel weglaten van een gaatje in het IML etiket omzeilde Moens Mouldings een kwart eeuw geleden het patent van de eerste in mould labeling verpakking. Het etiket werd in eerste instantie in de matrijs gelegd en vervolgens sloot de matrijs om de vloeibare poly propyleen door vanaf de buitenzijde in te spuiten. Een dicht IML-etiket (zonder inspuitgaatje) maakte het mogelijk om vanaf de binnenzijde aan te spuiten. Een techniek die spuitgieters tegenwoordig nog steeds toepassen.
‘Dit is een game changer in de IML-markt.’
‘Sinds het van binnen aanspuiten van de verpakking heeft er niet veel vernieuwends plaatsgevonden in de IML-markt’, zegt Wim Moens, algemeen directeur Moens Mouldings. ‘Onze nieuwe ontwikkeling brengt daar verandering in. Zonder robot (in-en uitname) gaan we van een cyclustijd van 4 á 5 seconden naar 1,3 seconden. Dit is een game changer in de IML-markt.’
Later dicht
De nieuwe spuitgiet-technologie van Moens is gebaseerd op het eerder inspuiten van de matrijs. Bij de bestaande technologie brengt een robotarm het etiket in, sluit de matrijs en wordt er vloeibare polypropyleen onder hoge druk ingespoten. Hiervoor moeten eerst de twee matrijsdelen met hoge hydraulische kracht worden gesloten. Als het kunststof bakje is afgekoeld, pakt dezelfde robotarm het bakje uit de matrijs en brengt tegelijkertijd weer een nieuw etiket in. Het gehele proces duurt per verpakking zo’n 4 tot 5 seconden.
Bij de nieuwe IML-technologie start de machine al met het inspuiten van de polypropyleen als de matrijs nog net niet helemaal gesloten is. De matrijs staat bij wijze van spreken nog op een kiertje, zo’n 2 mm. Hierdoor is er geen hoge druk nodig bij het inspuiten, kan de kunststof sneller de matrijs in stromen en is er fors minder sluitkracht nodig. De inspuitdruk gaat van gemiddeld 1.500 bar terug naar zo’n 500 bar. Een grote besparing op het energieverbruik. De nieuwe techniek kent ook een zeer snelle cyclustijd van 1,3 seconden (zonder robot) en als kers op de taart: de verpakkingen zijn dunner en nauwkeuriger dan de bestaande IML-verpakkingen. De tolerantie bij krimp gaat van 1,5 tot 1,8 % naar slechts 1,1 %.
De ICM techniek is door MM zover verbeterd dat er praktisch geen koeltijd meer ingesteld hoeft te worden.
Alleen maar voordelen, lijkt het. Maar de bestaande robotarmen die zo’n 12 tot soms wel 20 kilogram wegen, zijn niet sneller dan 1,2 -1,5 seconden. Dat zou dus de netto cyclustijd van 1,3 seconde gaan verdubbelen naar 2,6 seconden.
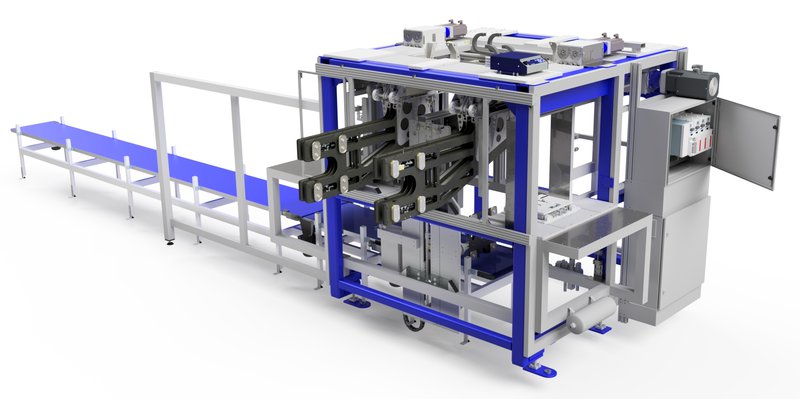
Vanaf nul
‘Er bestond in de IML-industrie geen robotarm die zo snel is dat hij binnen 0,6 seconden heen en weer beweegt tussen de matrijs’, zegt Wim Moens. ‘Onze R&D-afdeling is daarom vanaf nul begonnen met de ontwikkeling van een totaal nieuw robotconcept. De ontwikkeling heeft zo’n acht maanden geduurd waarvan de meeste tijd is gaan zitten in de robotarm.’
Om fors gewicht te besparen hebben de engineers de robotarm opgedeeld in twee dunne robotarmen van carbon en 3D geprint materiaal en is het totale gewicht gereduceerd naar 800-1000 gram.
‘Dit hele systeem is in staat om veel sneller de heen-en weerbewegingen te maken omdat wij bijna geen gewicht hoeven te verplaatsen. In plaats van 10 tot 12 kg halen we ongeveer totaal 1 kg tot 2 kg heen en weer. We halen een versnelling van 20 G. Dat is enorm snel.’
De spuitgieter bouwt de IML-robot helemaal zelf in eigen huis. Aan de hand van een filmpje toont Wim Moens hoe de IML-robot werkt. Hierin is te zien dat de robotarm met één beweging het etiket inbrengt en tegelijkertijd het gespuitgiette bakje uit de matrijs wegneemt.
Voordelen
‘Deze nieuwe IML-techniek zorgt dat IML-verpakkingen dunner, lichter, nauwkeuriger en goedkoper worden’, vat Moens samen. ‘Daarnaast is er voor de productie minder energie en kunststof nodig. Gezien al het nieuws rondom kunststof verpakkingen is dit een mooi voorbeeld van duurzaamheid. Je kan hiermee veel dunnere verpakkingen maken met behoud van functionaliteit. Je praat ook nog eens over een mono-materiaal toepassing. Dit is echt een duurzame oplossing.’
Moens verwacht dat de eerste toepassingen begin dit jaar op de markt komen. Naast de bakjes is het ook mogelijk om met de nieuwe technologie deksels te produceren. ‘Deksels die nu vacuüm worden gevormd in PS, kunnen wij nu met eenzelfde wanddikte in PP maken. Onze nieuwe IML-techniek verbeter niet alleen de huidige verpakkingen, maar het boort ook nieuwe markten aan.’
Meer artikelen
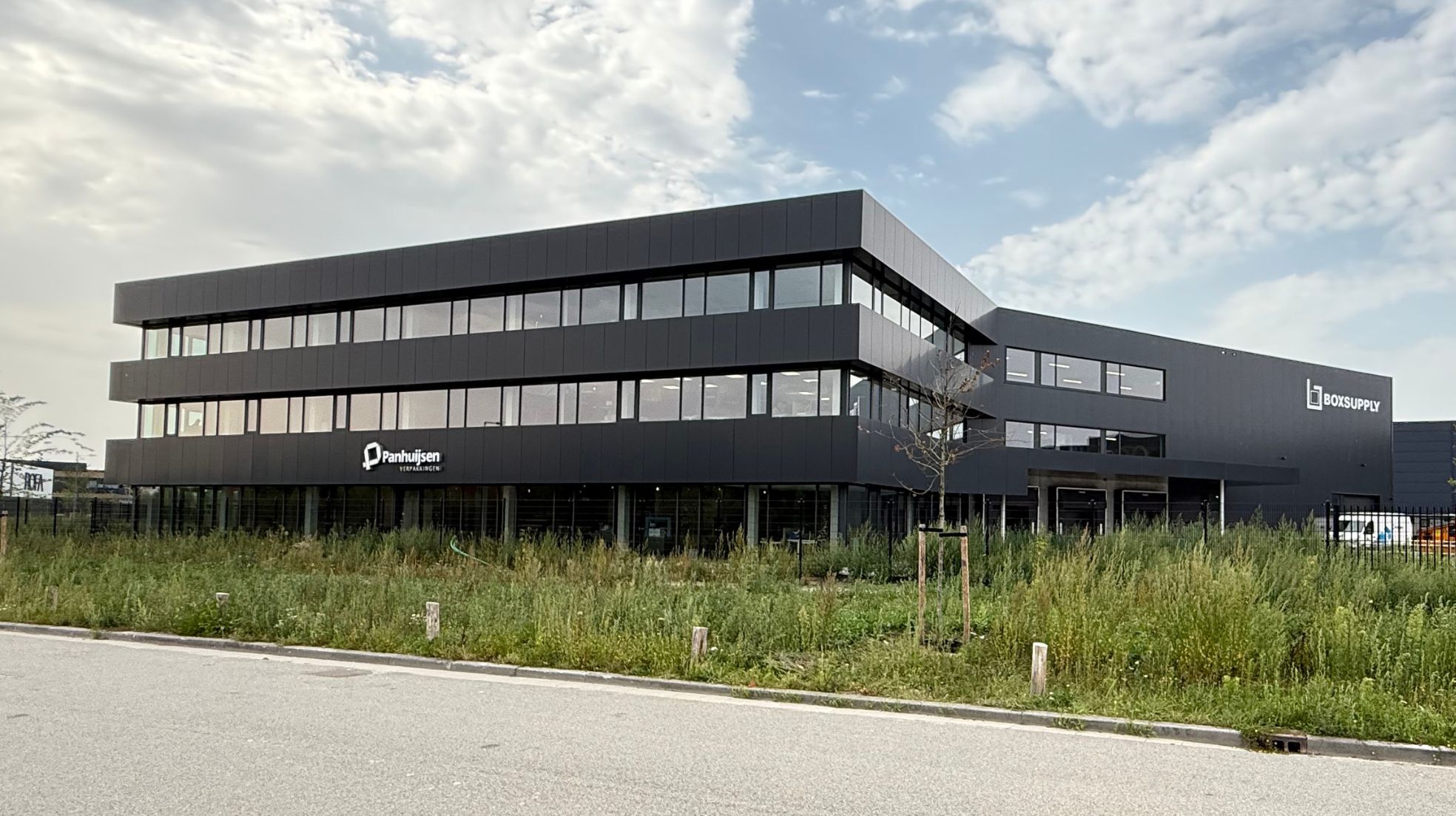
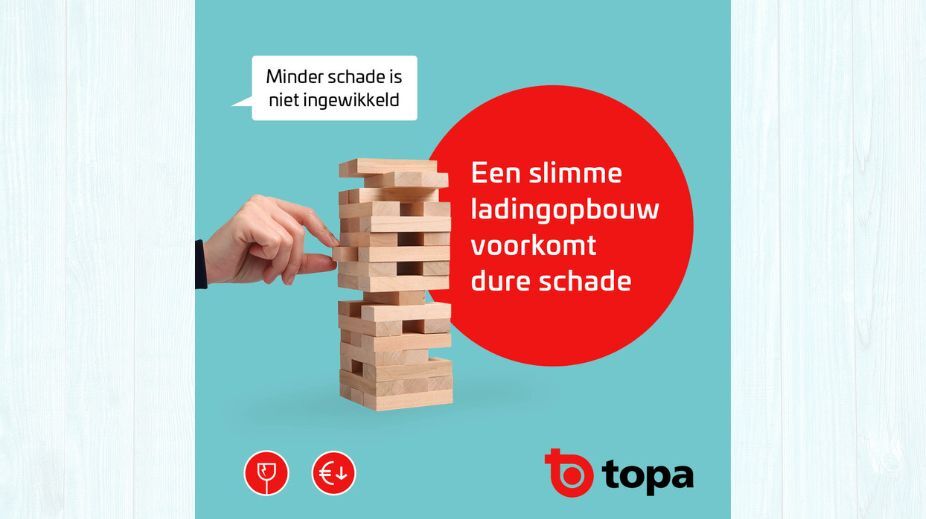
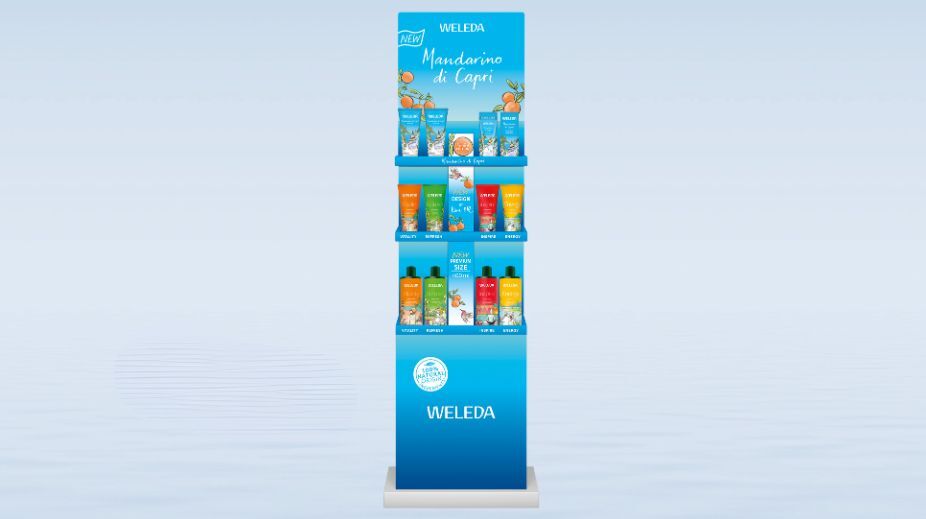
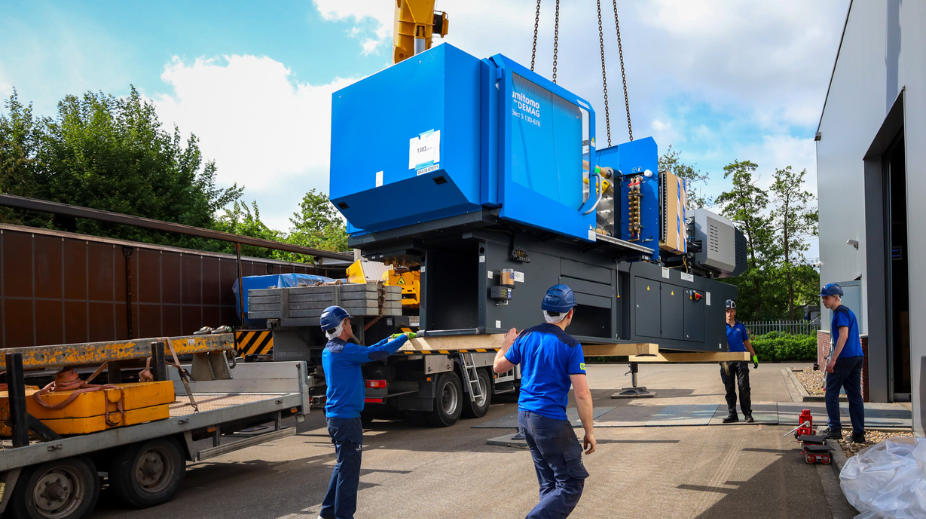
Gerelateerde artikelen
Panhuijsen verhuist en investeert in sneller en flexibeler produceren
Panhuijsen Verpakkingen is verhuisd naar een nieuw, modern pand op bedrijvenpark T58 in...
Zó maak je elke pallet stabiel en schadevrij
Een pallet die onderweg verschuift, indeukt of zelfs omvalt. Op het eerste gezicht lijkt het een...
STI Group speelt in op zomerseizoen met displayontwerp
STI Group heeft voor Weleda een nieuw display ontworpen dat inspeelt op de zomereditie Mandarino di...
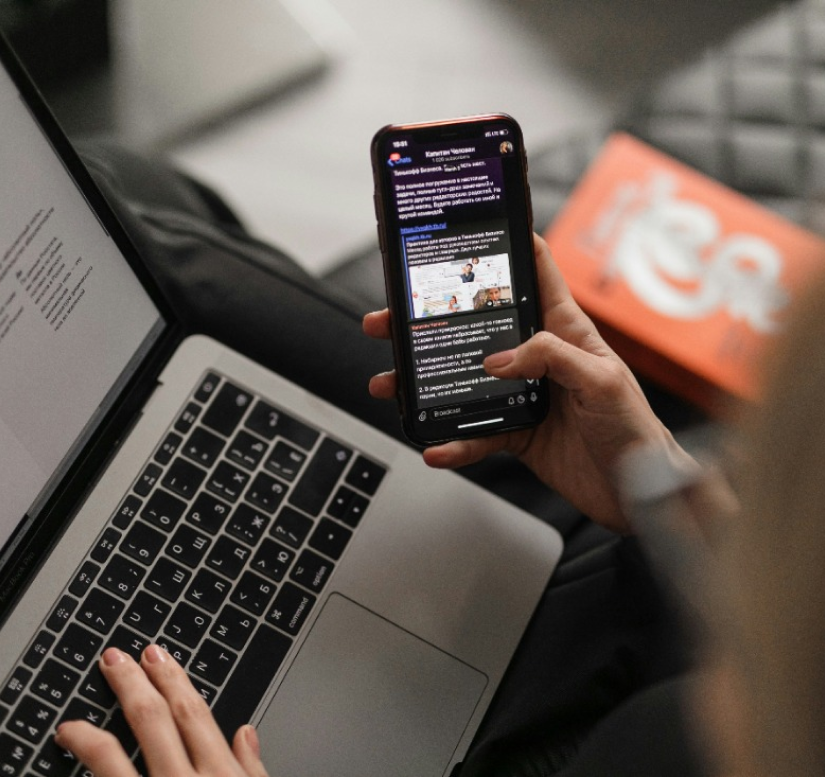
VM nieuwsbrief
- Blijf op de hoogte met het laatste nieuws uit de verpakkingsindustrie
- Techniek, duurzaamheid, design en meer
- Gratis in jouw inbox