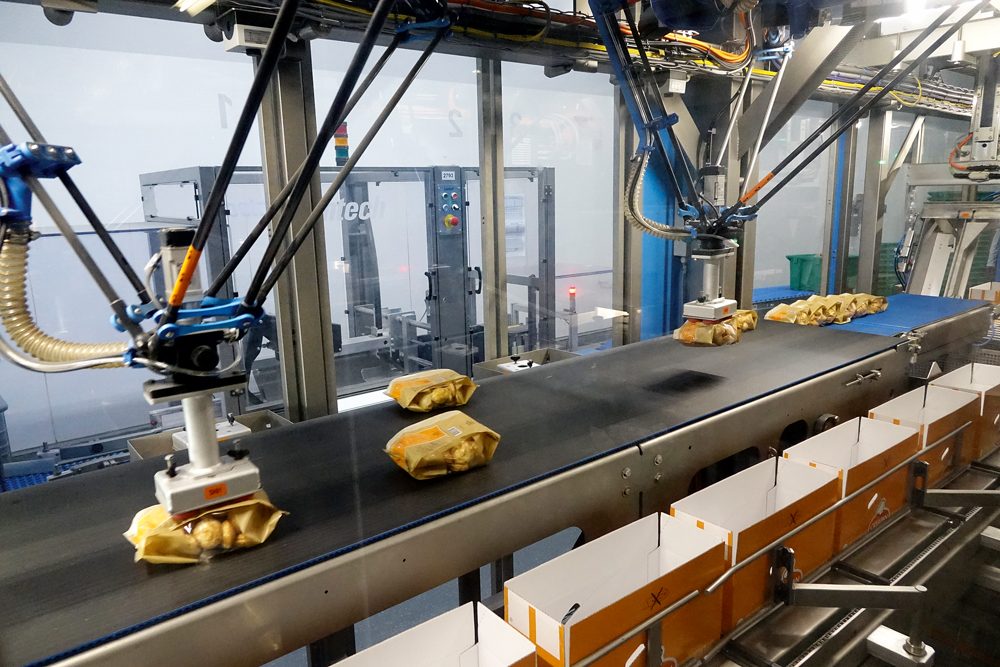
BluePrint Automation automatiseert pannenkoeklijnen
Pannenkoekenfabrikant Cérélia in Sliedrecht heeft het afgelopen jaar drie automatiseringsprojecten doorgevoerd. Belangrijke partner hierbij is BluePrint Automation. Naast het plaatsen van een aantal case packers en deltarobots verzorgde de machinefabrikant uit Woerden ook de complexe programmering en mechanische oplossing voor de zakaanvoersystemen.
Dagelijks komen er miljoenen pannenkoeken, poffertjes en pancakes uit de fabrieken van de internationale foodproducent Cérélia. De productie is verspreid over 12 productieplants wereldwijd. Eén van die plants ligt in Sliedrecht en komt voort uit de overname van De Bioderij in 2015. Het bedrijf produceert hier onder meer pannenkoeken en pancakes voor het bekende merk Jan en voor diverse private labels. De samenwerking met BluePrint Automation (BPA) dateert al uit de begintijd. Op de Macropack in 2000 legde De Bioderij-oprichter Jan Vink de eerste contacten. Hans Verhoeff, sales manager BPA, kan het zich nog goed herinneren. ‘In die beginperiode werd de eerste productielijn opgezet met een BPA Gantry robot. Inmiddels hebben wij wereldwijd meerdere case packers en robots geleverd voor het verpakken van zakjes en traytjes in dozen en voor het verpakken van naakt product.’
V.l.n.r.: Leendert-Jan van der Hout (Cérélia), Hans Verhoeff (BPA) en Michael Driessen (Cérélia).
Poffertjeslijnen
In 2022 besloot Cérélia haar poffertjeslijnen verder te optimaliseren en uit te breiden van drie naar vier case packers. De optimalisering was onder meer nodig, omdat Cérélia overstapte van dieptrekverpakkingen naar blokbodemzakken. Dit zorgde voor een flinke besparing van het kunststof verpakkingsmateriaal. De vierde case packer was nodig om zakjes met poffertjes naast liggend ook staand in SRP-dozen te verpakken. Het staand verpakken gebeurde handmatig. Voor deze automatisering heeft BPA de Spider 300v geleverd die met een speciale cassette de zakjes verzamelt, kantelt en rechtop in de doos zet. Deze Spider 300v kan snel omgesteld worden van liggend naar staand verpakken.
‘Het rechtop verpakken in SRP-dozen ging voorheen met de hand’, vertelt Leendert-Jan van der Hout, project engineer Cérélia. ‘Door het proces te automatiseren, hebben we twee arbeidskrachten bespaard per shift.’
Het buffersysteem bij de toastercake-verpakkingslijn bestaat uit vier carrousels met blauwe bakken (aan iedere zijde twee). Dit systeem kan de productie drie
minuten bufferen, zodat een foliewissel kan plaatsvinden.
Programmering
Het leveren en plaatsen van de nieuwe case packer was relatief simpel. Het ombouwen van de aanvoer naar de drie andere case packer-lijnen vergde echter veel engineeringswerk. Ook hiervoor werd BPA ingeschakeld. De machinebouwer verzorgde de programmering van de aanvoerbanden vanaf de inpakmachines naar de vier case packers. Het gaat om complexe situaties, waarin de verschillende aanvoerstromen vanaf bagmakers moeten worden verdeeld over de vier case packers. Dat vereist een goede synchronisatie met de machines in de lijn.
‘Je wilt dat het product zo goed mogelijk aankomt bij de case packer’, legt Van der Hout uit. ‘Er mogen bijvoorbeeld geen zakjes op elkaar liggen, want dan keurt het vision-systeem ze af en volgt een reject. Hoe beter de productaanvoer verloopt, hoe minder correcties er zijn. Dat vraagt om specifiek programmeerwerk. Dat hebben we bij BPA neergelegd, want met de programmeurs van BPA kunnen we lezen en schrijven.’
Pancake-lijn
Naast de poffertjeslijn is ook de pancake-verpakkingslijn geautomatiseerd. Twee BPA-deltarobots verzamelen sinds kort met speciale 3D-geprinte vacuümkoppen de pancakes en plaatsen die in topseal-trays. De BPA-robots halen hier een capaciteit van duizenden pancakes per uur. ‘Voorheen werd dit met de hand gedaan’, vertelt project engineer Michael Driessen. ‘Waar voorheen zes inpakkers aan de lijn stonden die duizenden pancakes per uur verpakten, hebben we voor deze lijn drie inpakkers per shift bespaard en is de line output flink verhoogd.’
De BPA Spider 300 voert de zakjes met poffertjes in een cassette die ze vervolgens staand in een SRP-doos plaatst.
Toastercakes bufferen
Een andere installatie, die van de toastercake-verpakkingslijn, was een forse uitdaging, aldus Michael Driessen. De oude lijn bestond uit vier BPA-robots die de toastercakes stapelden in stapeltjes van 3, 4 of 5, waarna 3 à 4 inpakkers ze in dieptrektrays plaatsten.
‘In drie shifts hadden we dagelijks 9 à 12 inpakkers nodig’, vertelt Driessen. ‘Deze lijn is nu geautomatiseerd met vier deltarobots. Het binnenbrengen van de robotlijn was een flinke klus, want de hele pui moest eruit, we moesten de Multivac-machine verplaatsen en de robot over bestaande lijnen tillen.’
De uitdaging bij BPA zat in de ontwikkeling van een nieuw buffersysteem voor de toastercakes, vertelt Hans Verhoeff. ‘De toastercakes komen met duizenden bij de robot aan. Om die te bufferen was de nodige programmering en een speciale constructie nodig.’
Het buffersysteem bestaat uit vier carrousels met kunststof bakjes aan weerszijden van de BPA-robot. Het kan de toastercakes tijdelijk bewaren als er een foliewissel van de dieptrekker plaatsvindt of als er een kleine storing is, bijvoorbeeld een etiketteerprobleem.
De buffer kan dan een productiegang van maximaal 3 minuten opvangen, zodat niet de hele lijn moet worden stopgezet. ‘Dit was een mooie uitdaging voor onze engineers’, zegt Verhoeff.
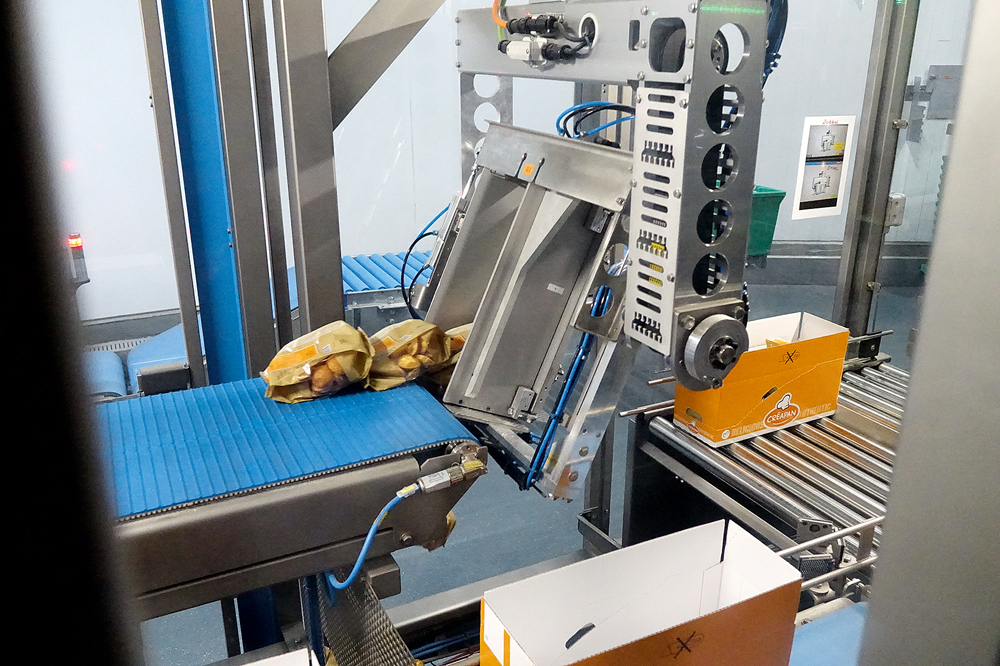
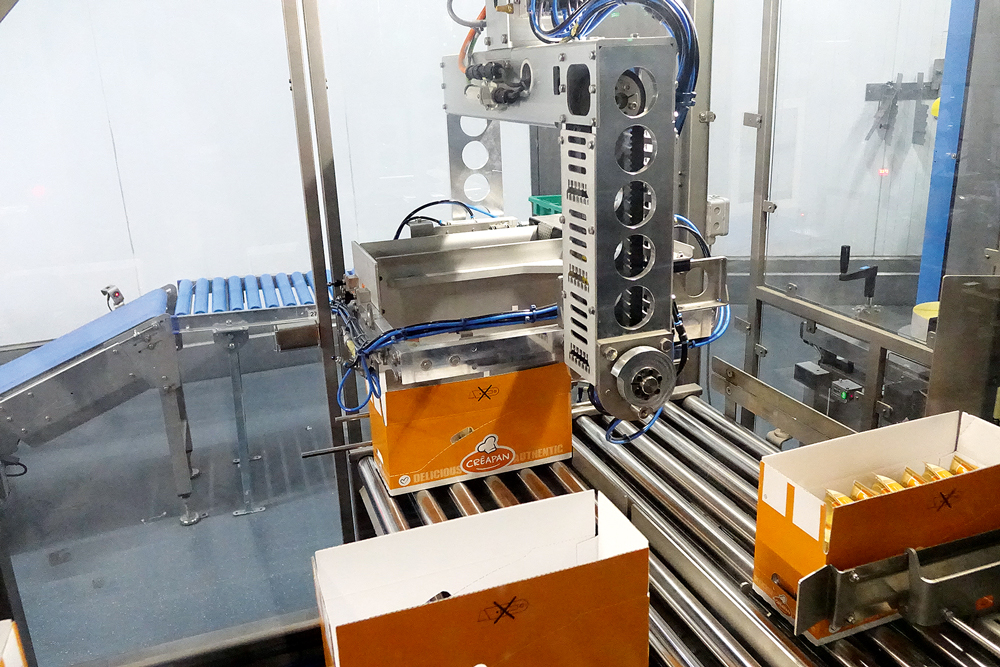
De BPA Spider 300 voert de zakjes met poffertjes in een cassette die ze vervolgens staand in een SRP-doos plaatst.
Dataverbinding
Michael Driessen kijkt met een goed gevoel terug op de drie projecten. ‘De installaties verliepen vlot en de service vanuit BPA is uitmuntend’, zegt hij. ‘Als ik ze bel, is er gelijk actie. Dat is ook nodig, want als wij problemen hebben en we staan stil, kost dat ons veel geld. Daarom vraag ik altijd aan onze machineleveranciers of ze willen zorgen voor een dataverbinding naar hun serviceafdeling, zodat zij op afstand mee kunnen kijken om de problemen op te lossen.’
‘Goede communicatie is essentieel’, bevestigt Verhoeff. ‘Dat zorgt voor een prettige samenwerking en is de basis voor een succesvol project.’
DIT ARTIKEL KWAM TOT STAND IN SAMENWERKING MET BLUEPRINT AUTOMATION.
Meer artikelen
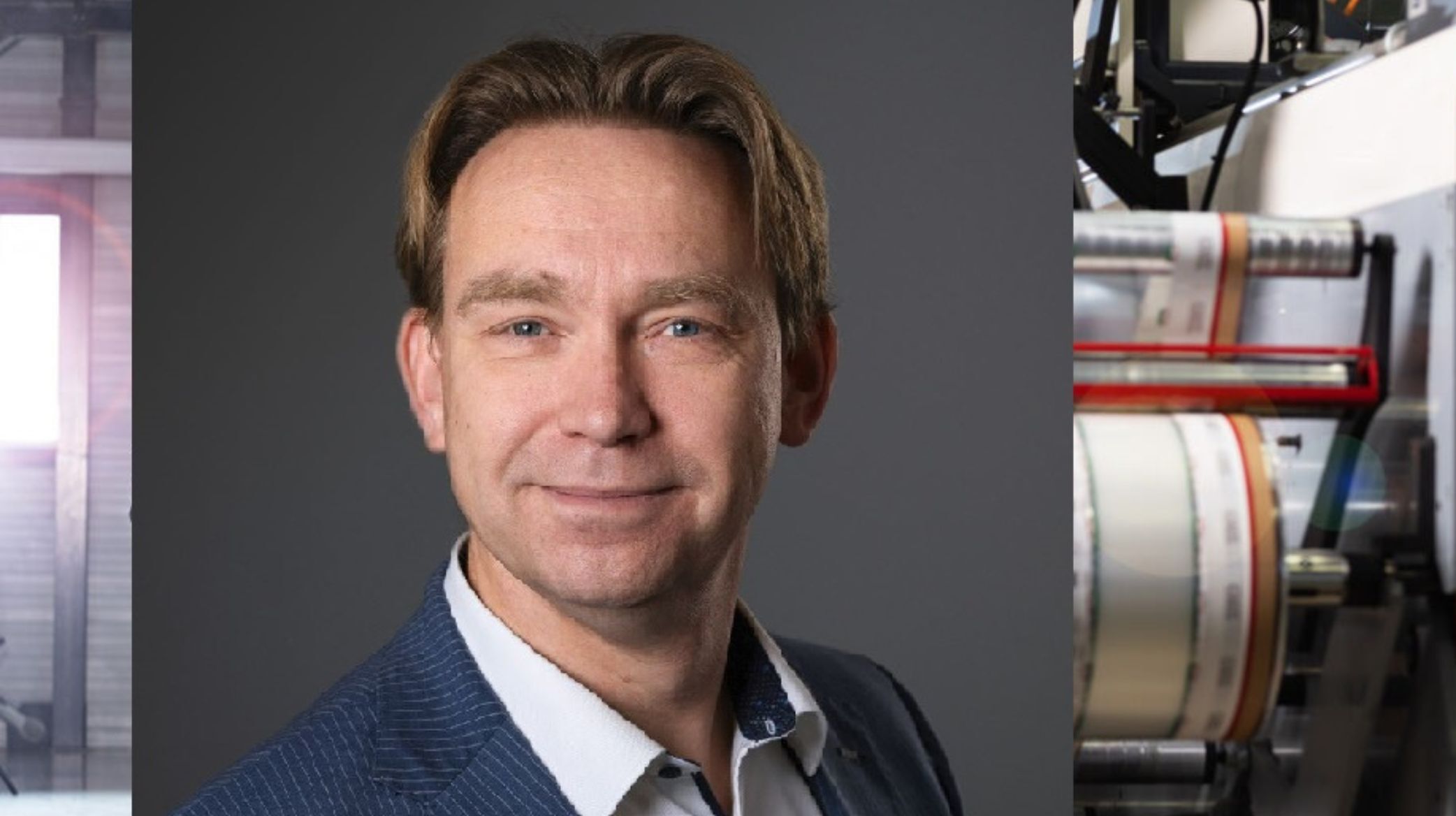
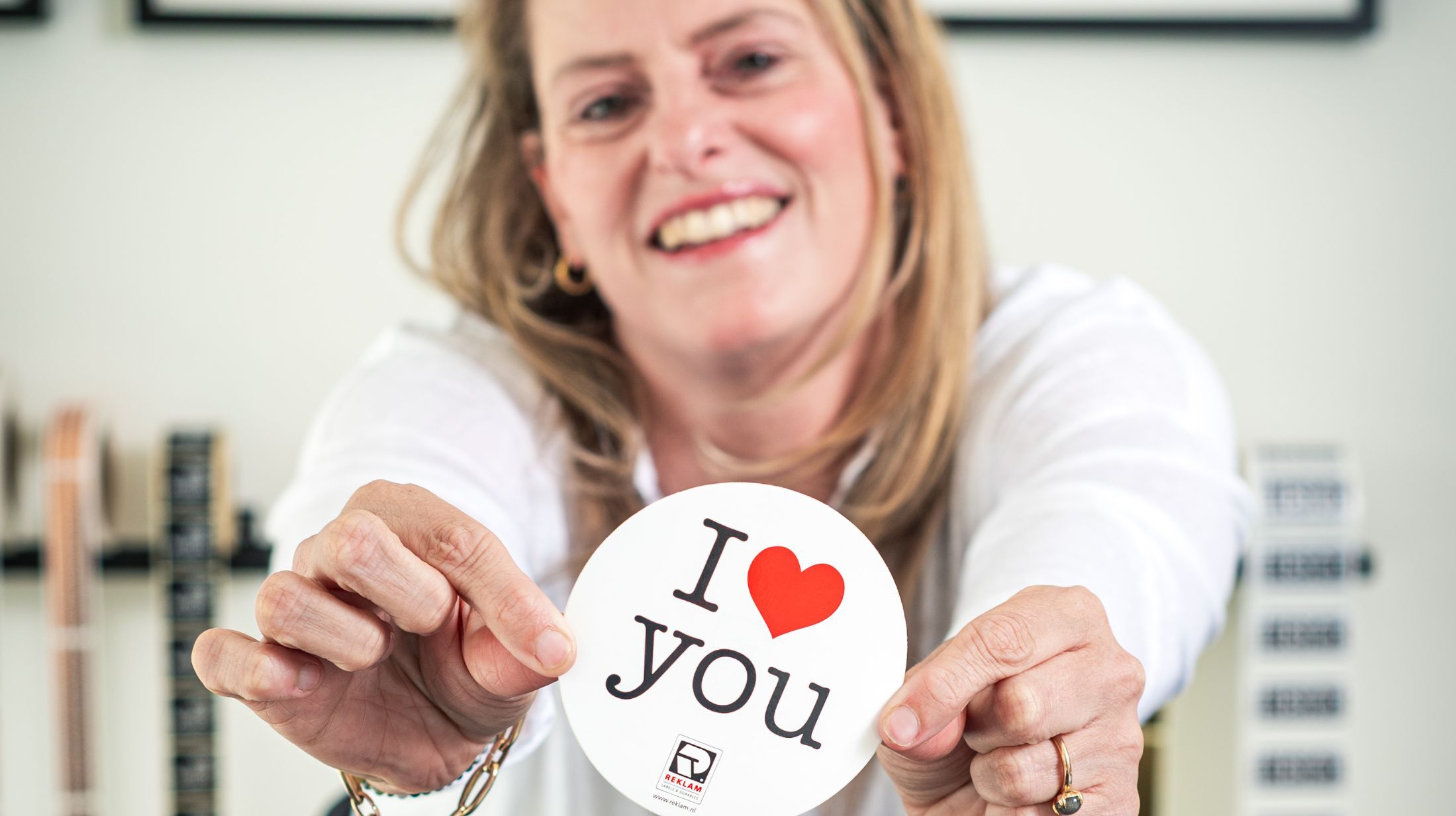
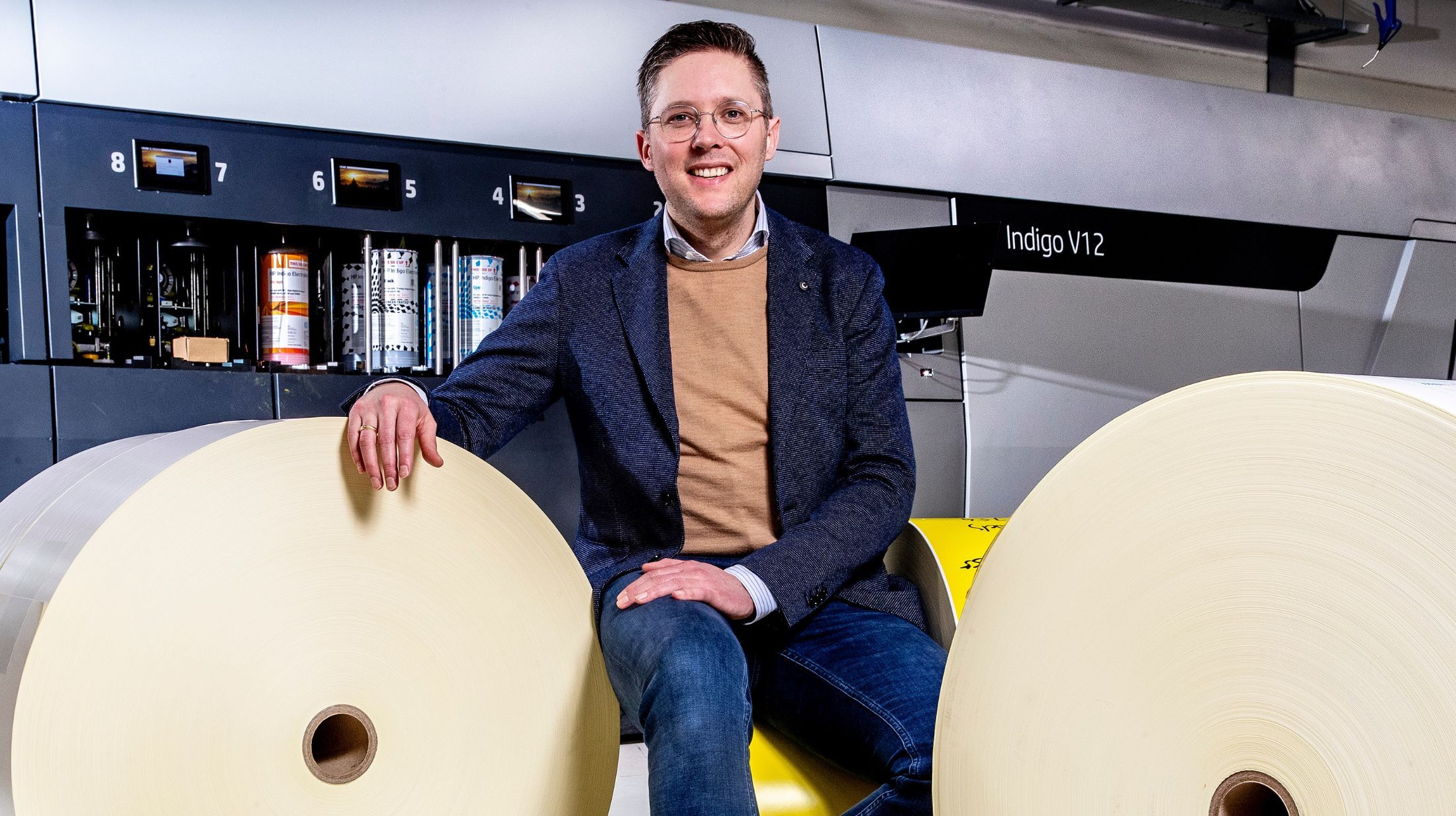
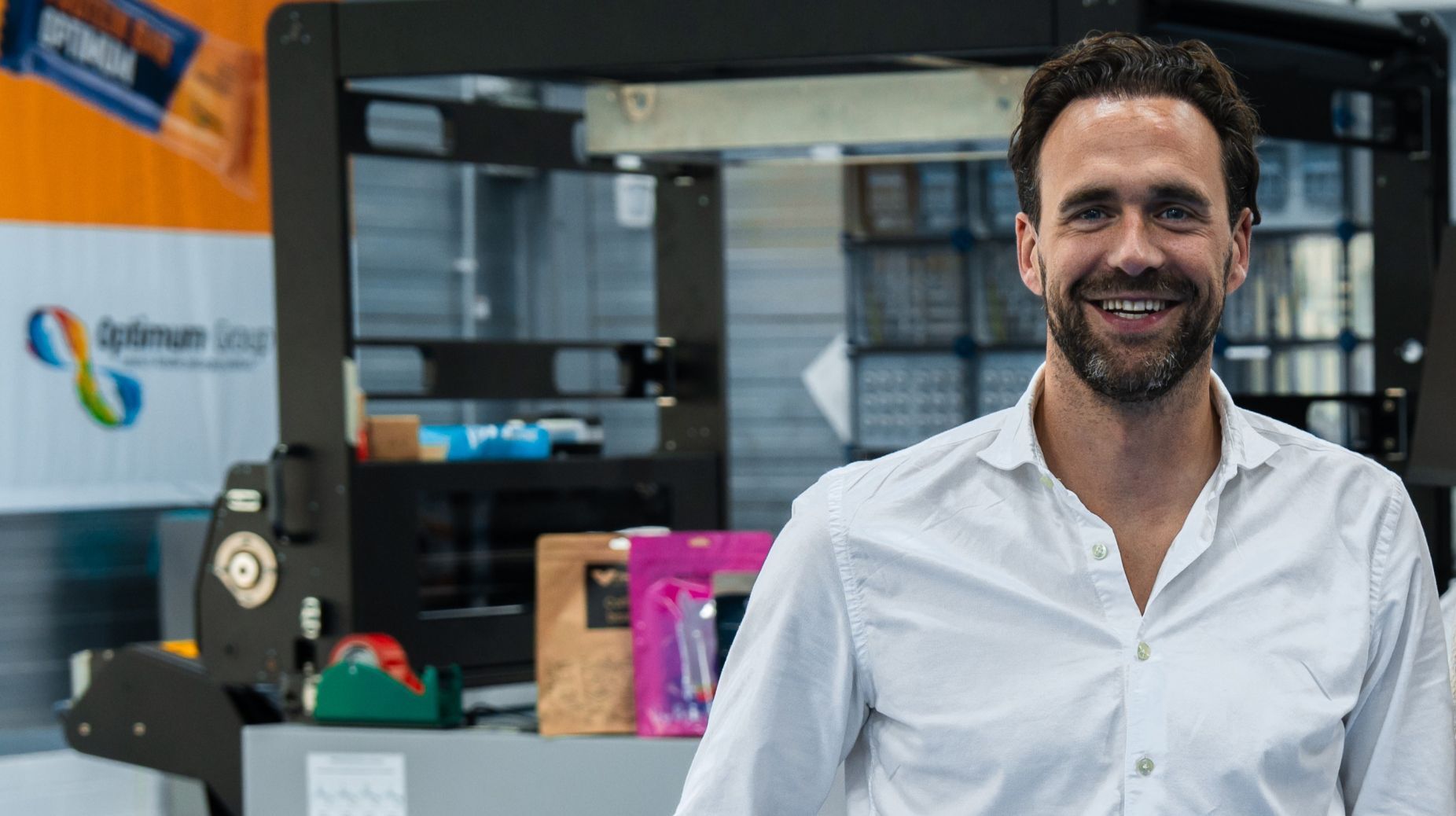
Gerelateerde artikelen
Jan-willem Vink van Geostick: ‘Wij leveren geen etiket, maar een oplossing’
Geostick produceert zelfklevende etiketten voor uiteenlopende sectoren. Het familiebedrijf kijkt...
Mabel Smit van Reklam: ‘Labels zijn steeds vaker een digitale informatiedrager’
De etikettenmarkt is volop in beweging. Nieuwe wetgeving, zoals de Packaging & Packaging Waste...
Roy Schoemaker van Eshuis: ‘Het gaat om het totaalplaatje’
De etikettenmarkt staat onder druk van nieuwe wetgeving, stijgende duurzaamheidseisen en toenemende...
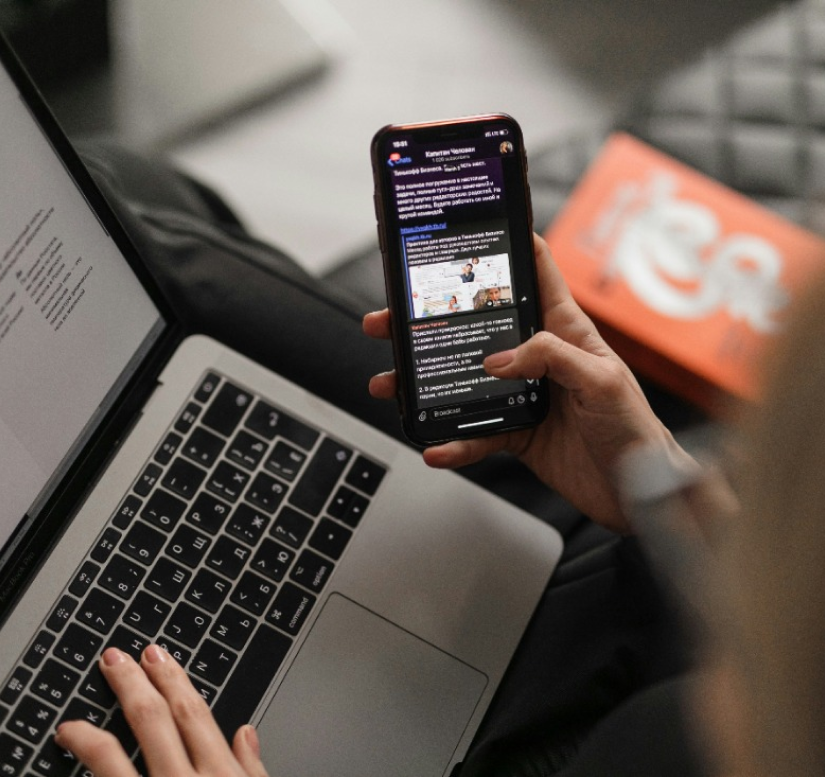
VM nieuwsbrief
- Blijf op de hoogte met het laatste nieuws uit de verpakkingsindustrie
- Techniek, duurzaamheid, design en meer
- Gratis in jouw inbox